
Testing & Quality Assurance
Materials Testing is performed for a variety of reasons and can provide a wealth of information about the tested materials, prototypes or product samples. The data collected during testing and the final test results can be very useful to engineers, designers, production managers and others.
EAG experts and consultants assist clients to assess & reach the following:
• Meeting requirements of regulatory agencies
• Selecting appropriate materials and treatments for an application
• Evaluating product design or improvement specifications
• Verifying a production process
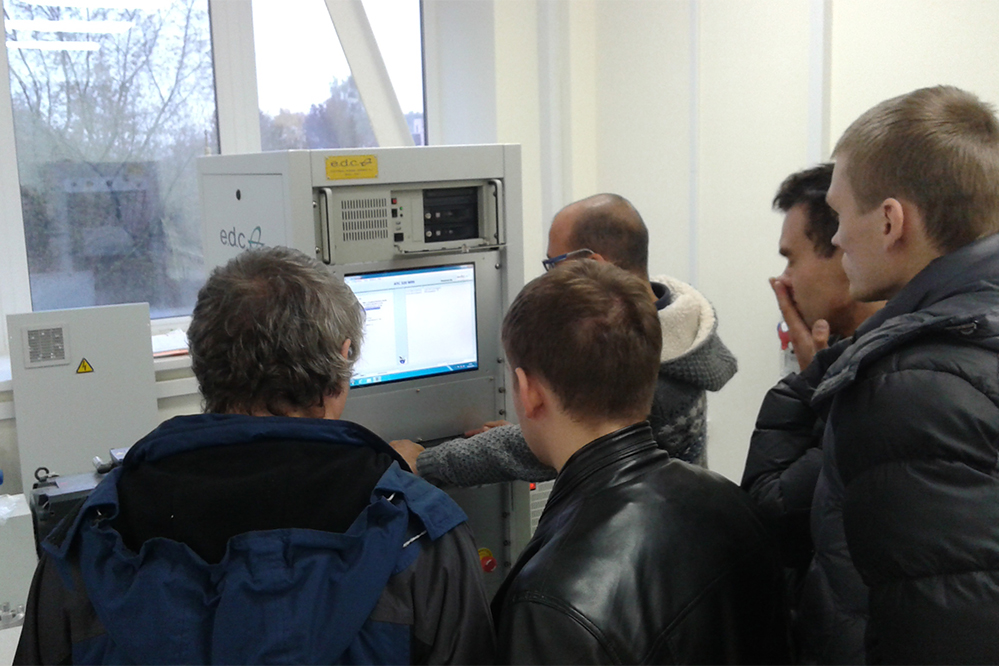
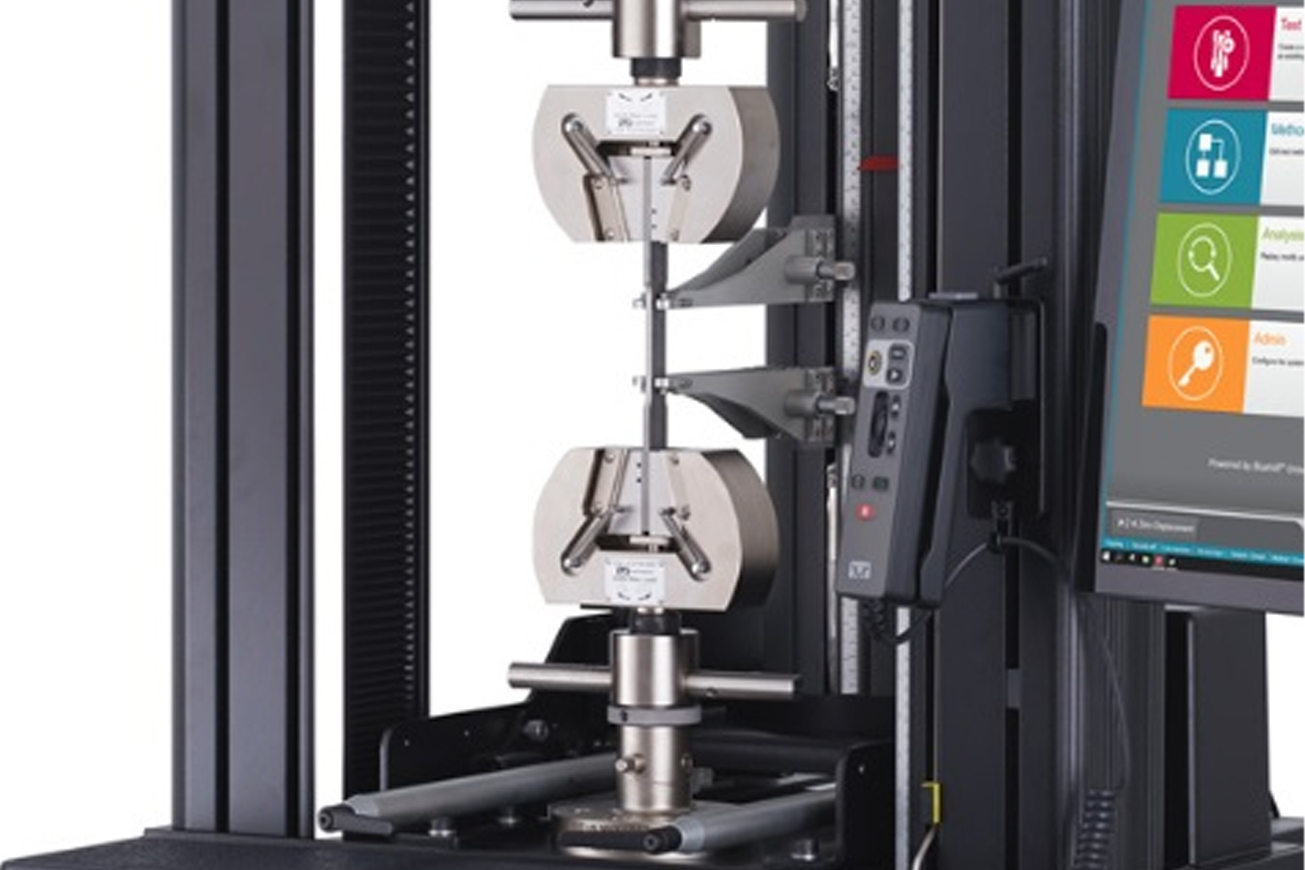
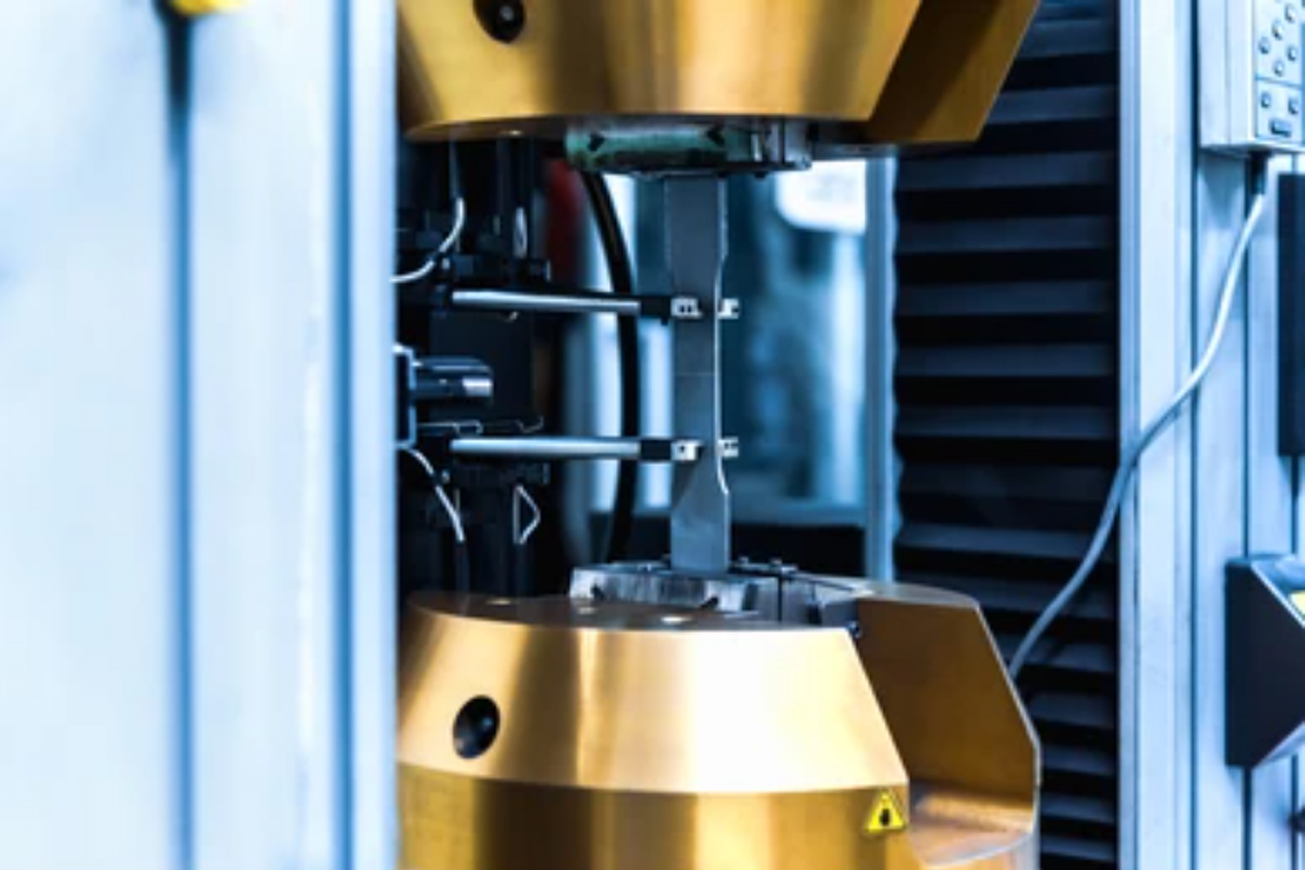
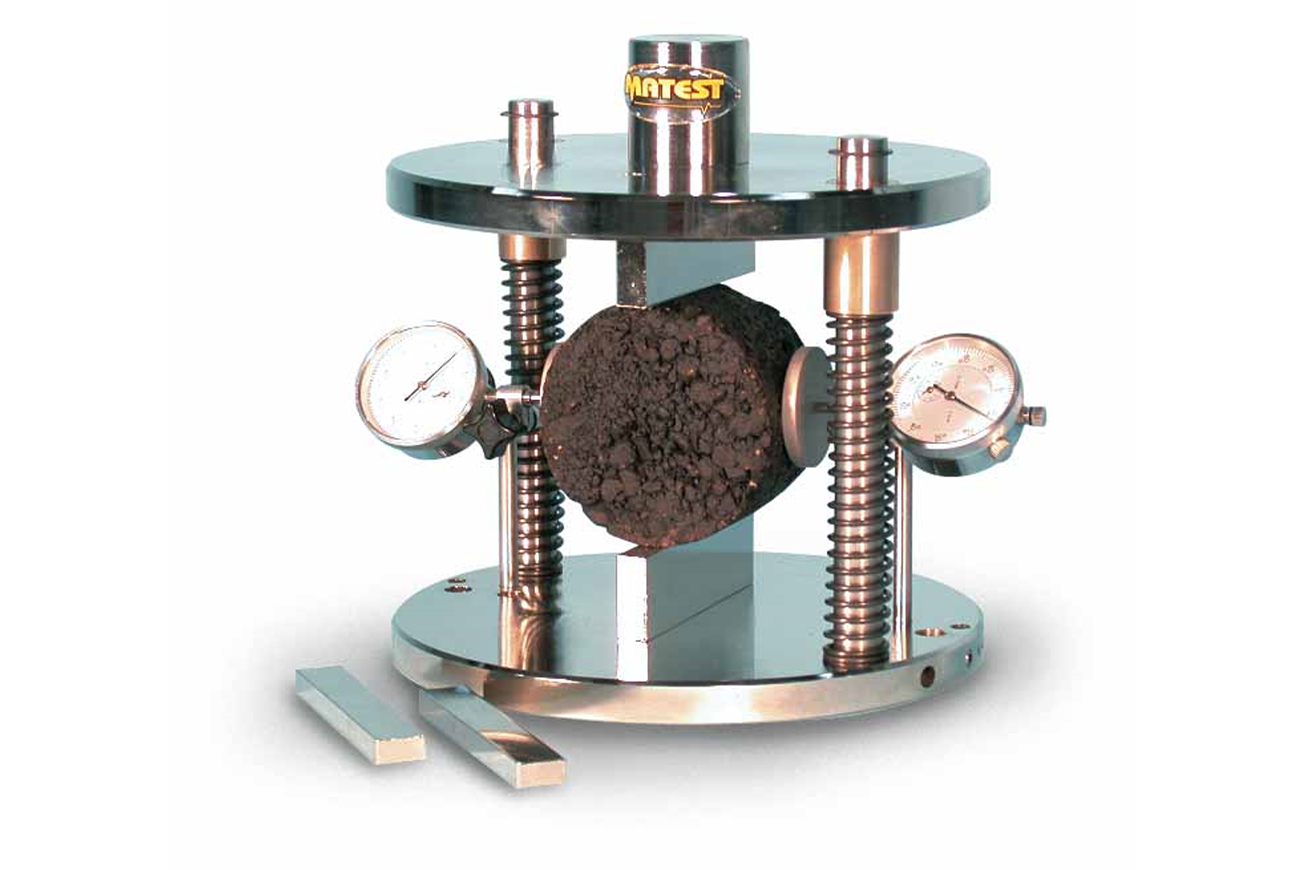
Many products are used in critical applications where a failure could result in extensive damage or injury. Some examples are manufactured fasteners and parts that have a vital role in maintaining the safety of aircraft, bridges, vehicles, nuclear reactors, military equipment and medical implants. In addition, many jurisdictions have adopted legislation restricting the use of hazardous materials.
In cases like these, governments and regulatory bodies set compliance requirements that must be met by manufacturers. Companies must adhere to these standards, which generally specify test procedures, to prove compliance.
The quality of material going into a manufactured product is as important as the reliability of the production process. Materials testing helps us to understand and quantify whether a specific material or treatment is suitable for a particular application.
Not only is testing commonly relied on for material selection and choosing a reliable supplier, but it is also frequently used as a verification process to be sure that material received from a new supplier is what was ordered. Material Testing may include methods that yield information about the structure or mechanical properties of the material. It may also make sense to verify the composition or elemental content of the material with an instrumental or classical wet chemical analysis technique.
It’s typical for a business to purchase mechanical testing services when specifying material for a new product design. Testing may be performed to evaluate mechanical properties such as strength, hardness, elasticity and fracture toughness. Corrosion testing can determine if the material will hold up under given conditions such as humidity or a salt water environment.
When an application requires more durable or more corrosion-resistant metals, this can often be attained with the addition of treatments. When appropriate, the material may be heat treated prior to testing to determine that the specified results have been achieved.
Testing is an essential part of both design and manufacturing processes, not only when safety is a concern, but also for any company committed to selling reliable products and minimizing damage and costs if problems do surface. Testing is often performed early on during product development to evaluate a planned production process. It can also be just as relevant to provide validation for final products on an ongoing basis. Various types of non-destructive testing services are used to evaluate finished products without causing damage to the items.
All building renovation or construction, and especially laboratory renovation or construction, involves many issues that must be resolved and many decisions that must be made.
ENVIRONMENTAL HEALTH AND SAFETY:
Throughout the planning, design, and construction phases of a laboratory renovation or construction project, careful attention to EH&S issues is essential to ensure that the facility can be built and occupied. EH&S issues influence every major decision—from site selection to suitability of the building for occupancy. Further, careful attention to these issues is important in interactions with the neighboring community, which may be passionately concerned about the local impact of a chemical facility.


ENVIRONMENTAL HEALTH AND SAFETY:
Throughout the planning, design, and construction phases of a laboratory renovation or construction project, careful attention to EH&S issues is essential to ensure that the facility can be built and occupied. EH&S issues influence every major decision—from site selection to suitability of the building for occupancy. Further, careful attention to these issues is important in interactions with the neighboring community, which may be passionately concerned about the local impact of a chemical facility.
Codes and Regulations:
Construction or renovation of a laboratory building is regulated mainly by state and local laws that incorporate, by reference, generally accepted standard practices set out in uniform codes. Box 3.1 lists the kinds of codes that affect most laboratory construction projects. The codes are usually administered at a municipal or county level but some locations may be administered at a regional level.
Types of Code Requirements That Affect Most Laboratory Construction Projects:
• Ventilation—to maintain comfort and occupational health.
• Fire prevention—to detect and suppress fires, in part by limiting quantities of flammable and hazardous chemicals.
• Emergency power supply—to maintain the operation of vital life-safety systems such as egress lighting, fire detection, and protection systems during an electrical interruption.
• Control of hazardous gases—to reduce the risk from and to control accidental releases of gases.
• Building height—to limit the height of laboratory buildings based on chemical usage.
• Seismic requirements—to reduce the hazards posed by earthquakes.
• Environmental issues.
• Managing Hazardous Waste.
• Controlling Chemical Vapor Emissions.
• Controlling Liquid Effluents.
• Health issues.
• Laboratory chemical hoods.
• Laboratory ventilation system.
• Hazardous Operations.
• Access control.
• Safety issues.
• Design considerations.
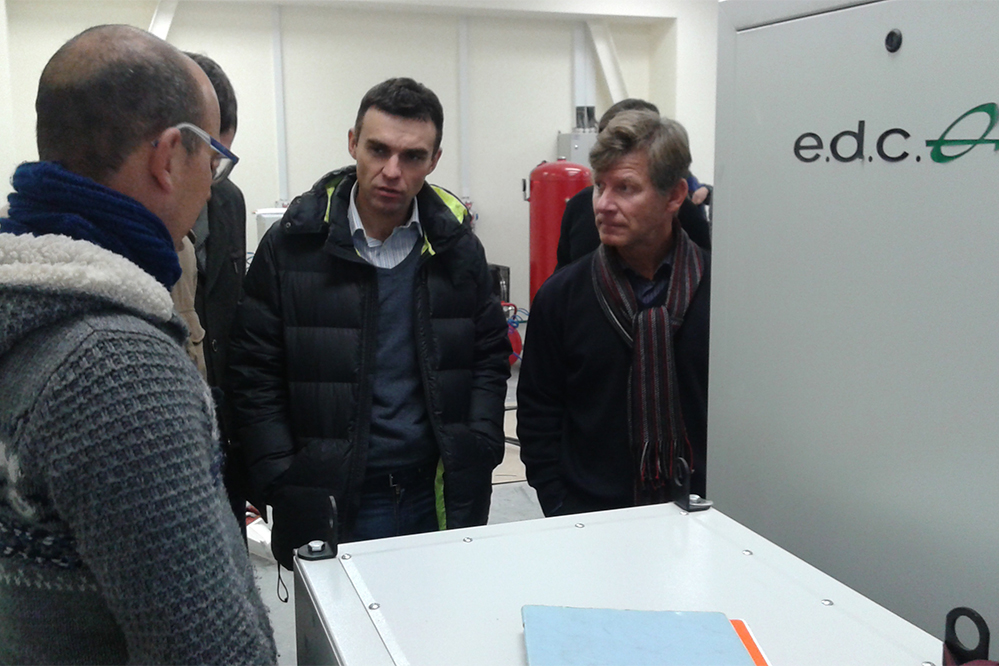
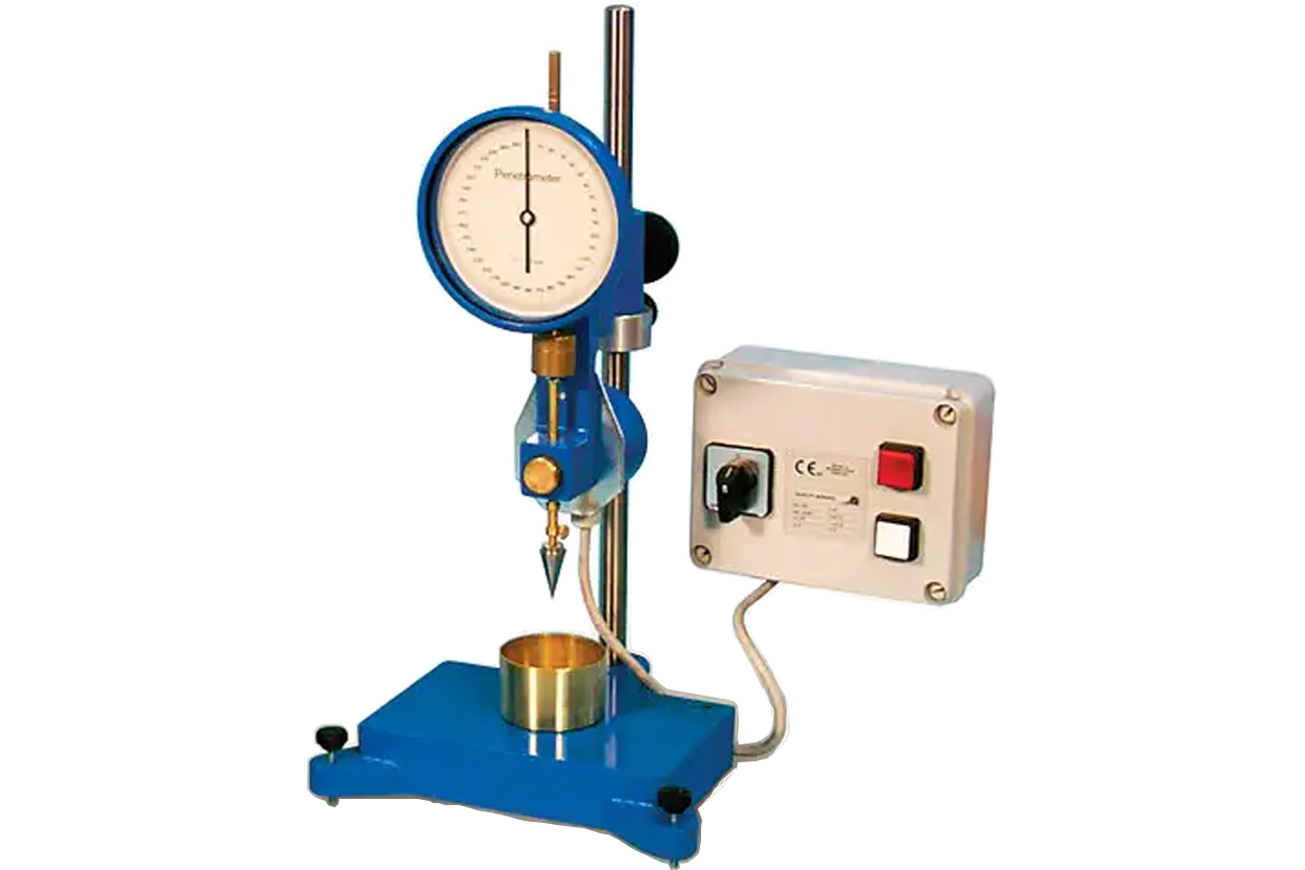
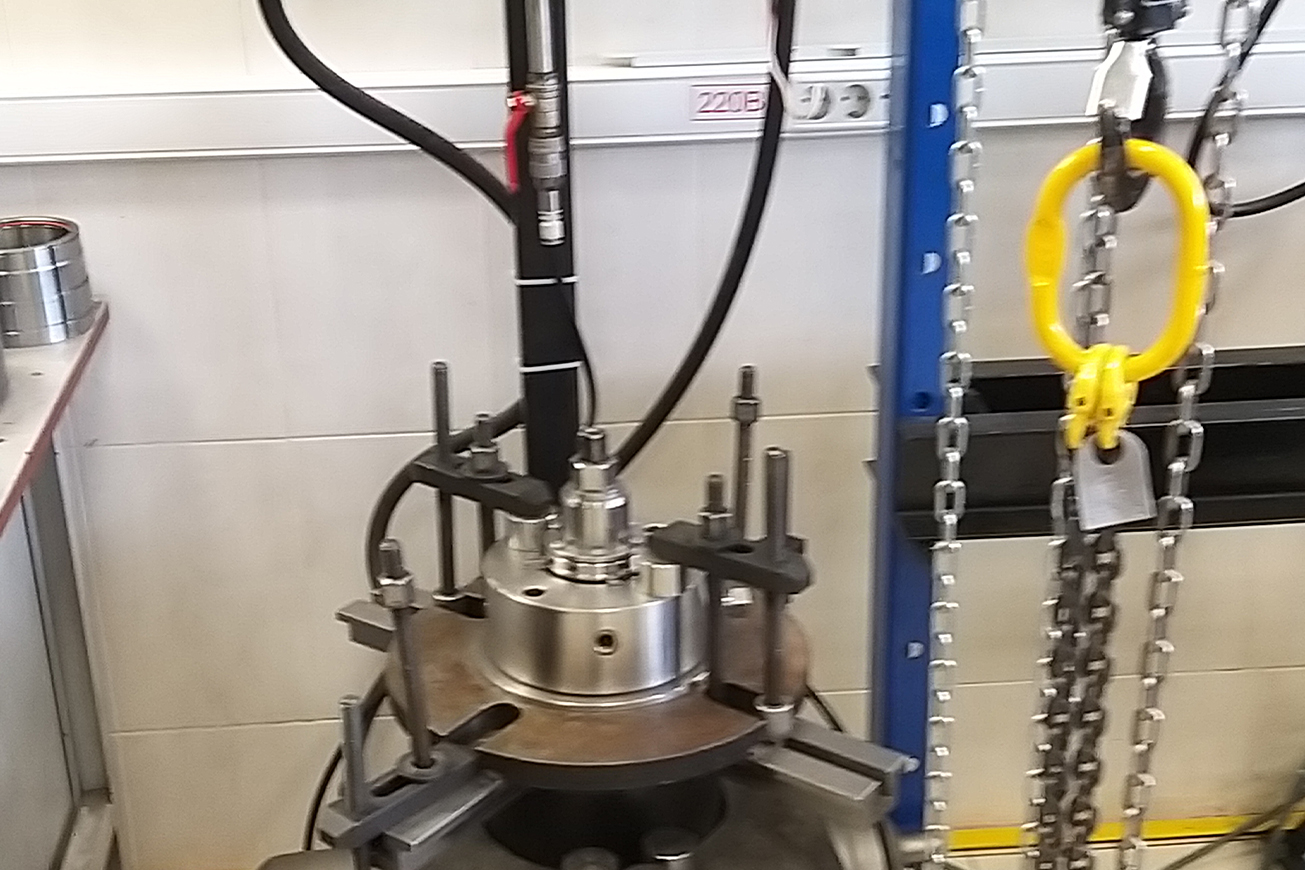